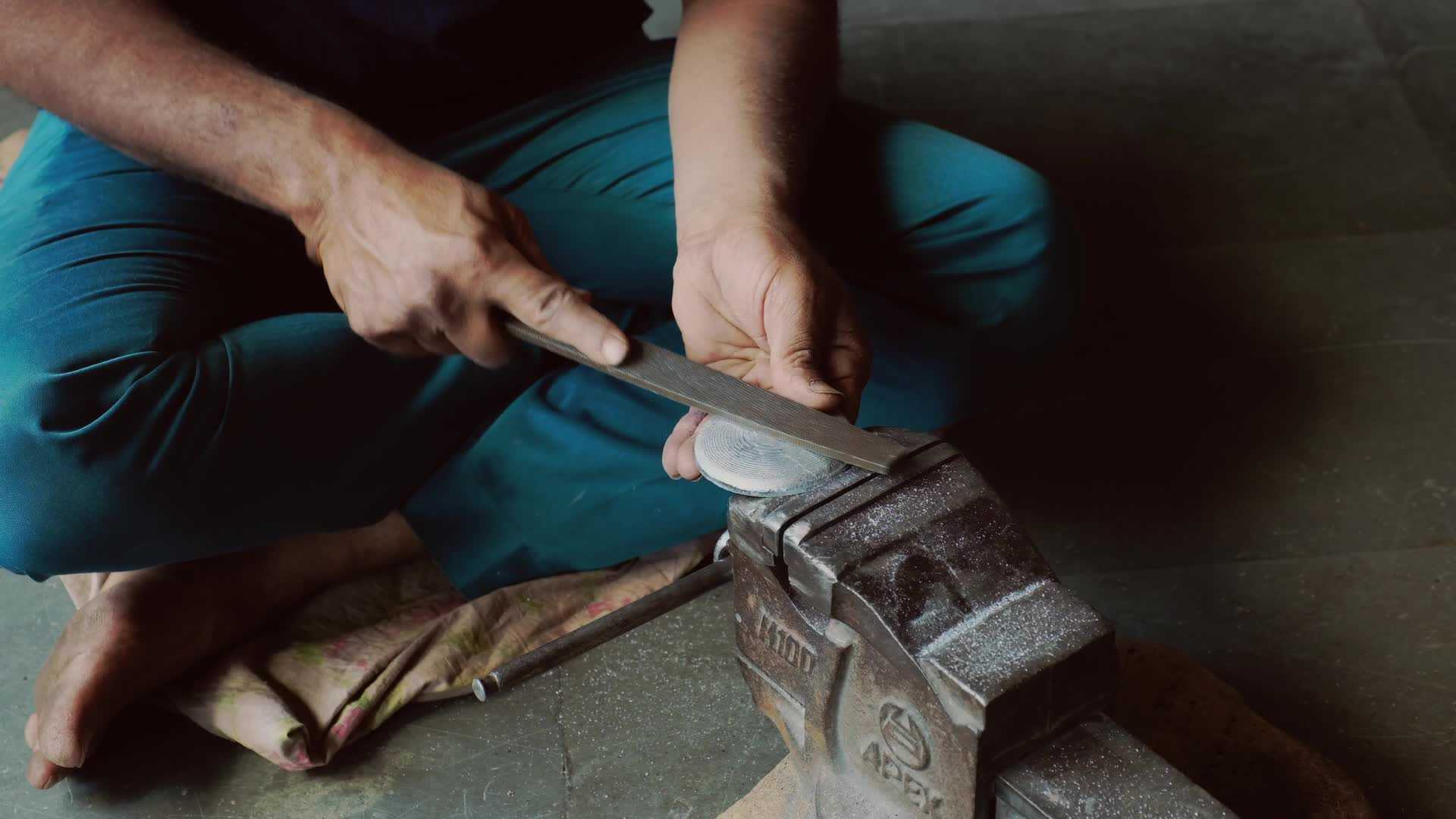
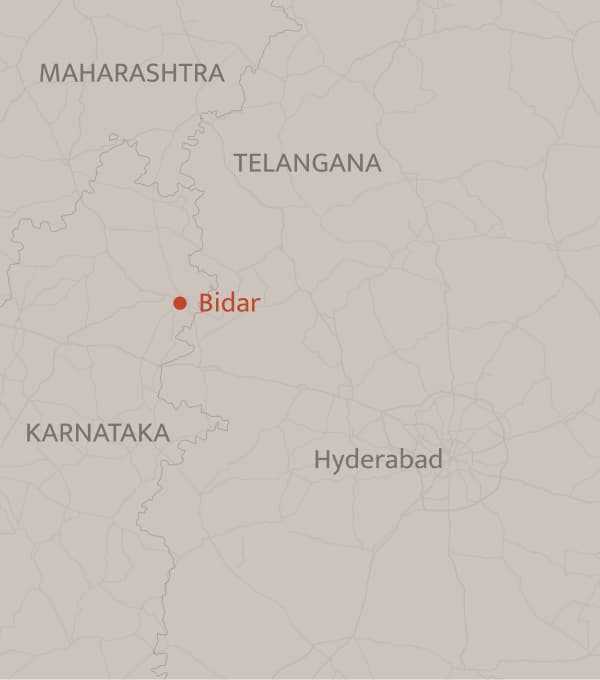
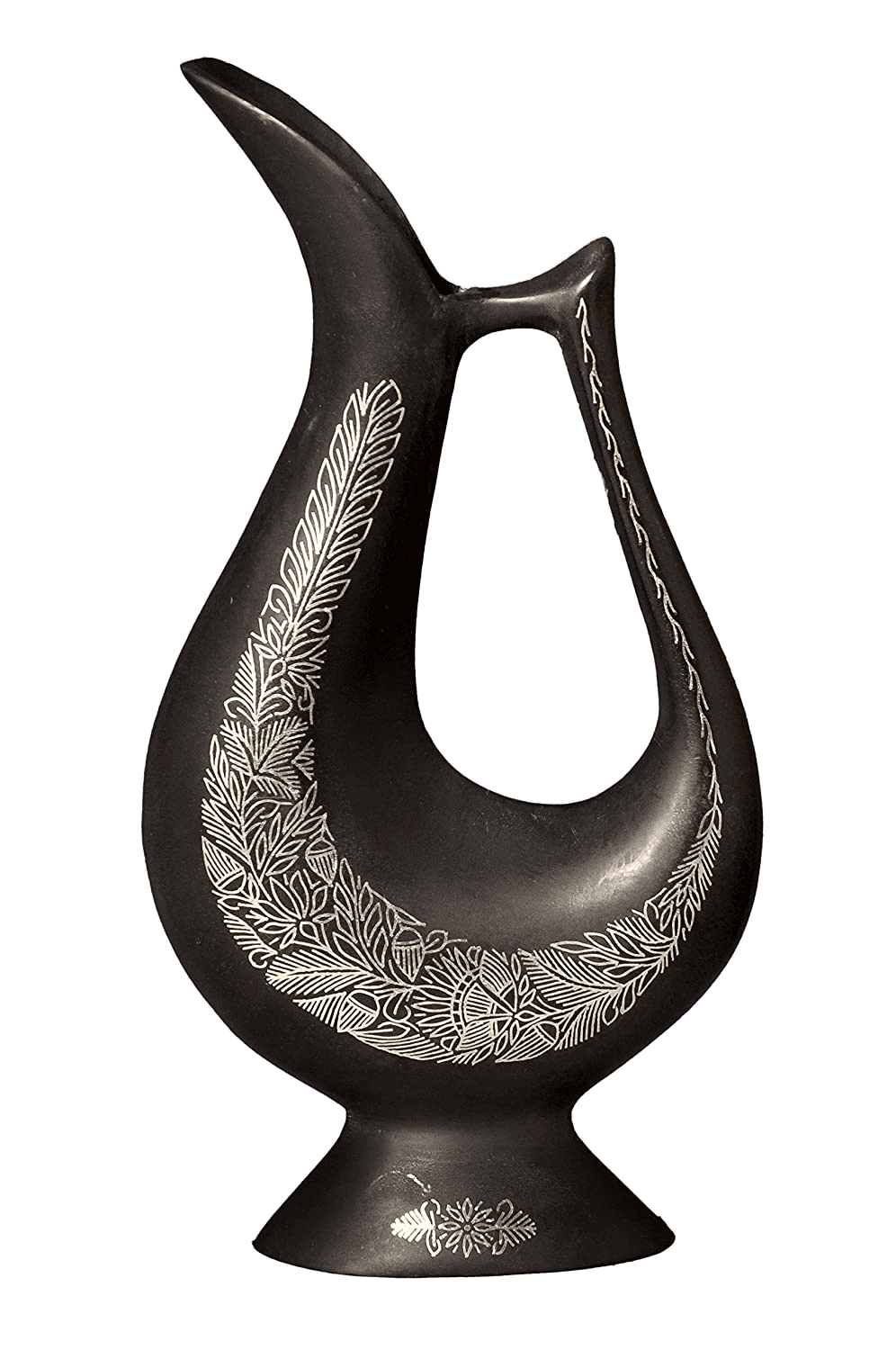
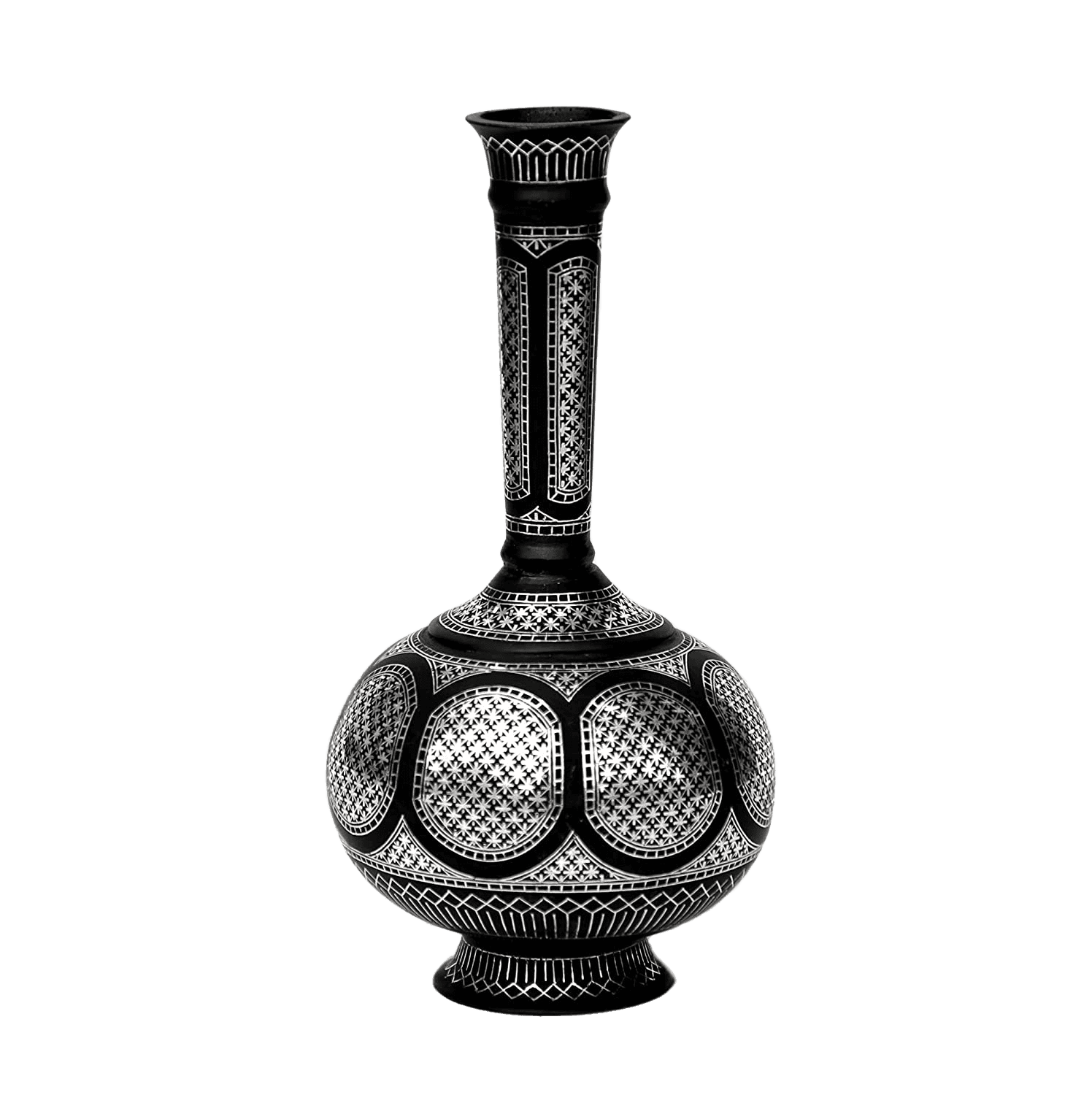
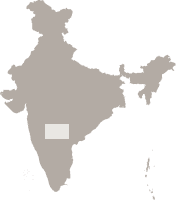
Bidri
A Royal Tradition
Bidri, the distinctive metal inlay craft of Karnataka, embodies 600 years of traditional practices, processes, and materials.The craft is said to have originated in the royal courts of Persia, from whence it travelled to India and flourished under the patronage of the Bahmani Sultans who ruled Bidar in the 14th and 15th centuries. Here, skilled artisans merged local craftsmanship with Persian influences to create a unique art form that is now recognised as distinctly Indian.
The Bidri Process
A Symphony of Skill and Materials
The enduring allure of Bidri can be attributed to the unbroken lineage of artisanal skills, passed down from generation to generation of craftspeople. The craft gets its name from Bidar, an area in Karnataka, which is considered home to this art.
The Craftspeople
M. A. Rauf and team, who have been a part of this collaboration, are masters of the 600-year old practices of Bidri. They took on the challenge to reinterpret their craft. The fusion of their traditional techniques with modern design perspectives involved navigating different working styles and aesthetic preferences, leading them to new discoveries and innovative solutions.
The collaborative journey boosted the craft team’s pride in their artistry, realising that their handcrafted skills significantly contributed to the aesthetic allure of the final creations.